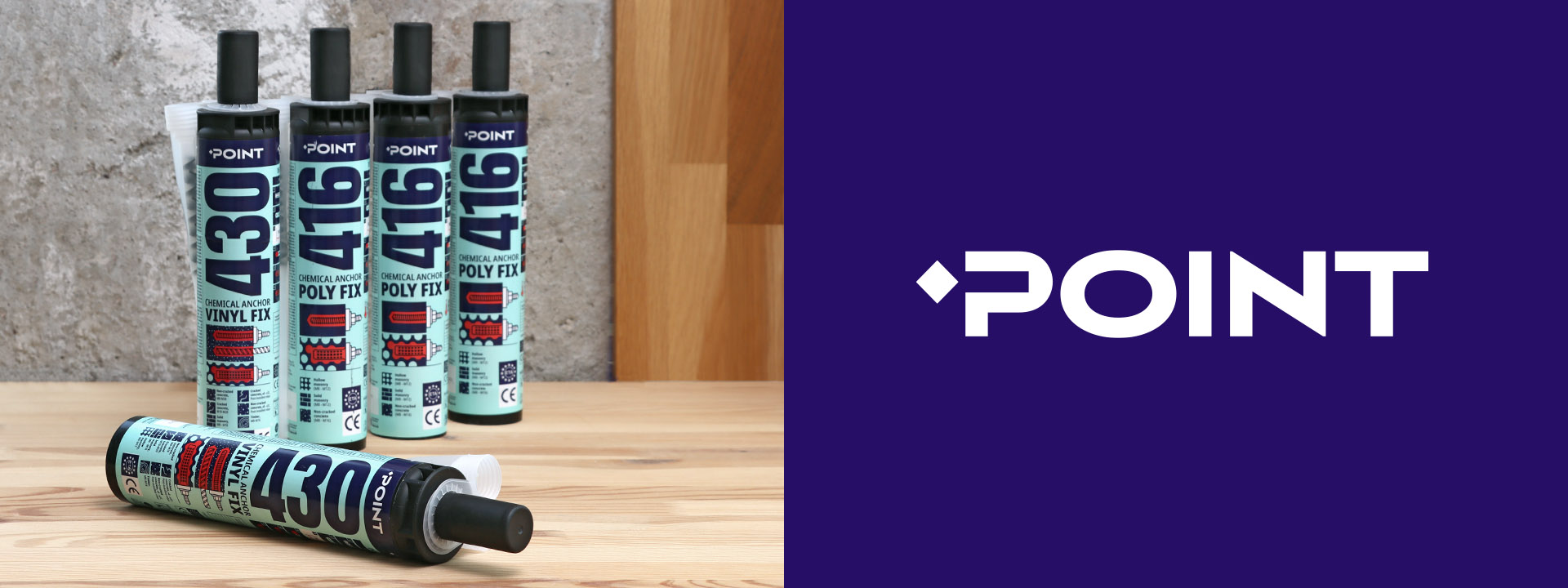
Many professionals have faced the challenge of securing construction elements that are able to withstand very heavy loads. They often need to decide whether a mechanical anchor will do, or should the fixture be secured with a chemical anchor instead. Increasingly, to be extra safe, they opt for the latter.
Mechanical anchors can fasten elements to concrete walls of almost any type: the sturdier the concrete, the easier it is to secure a fixture to it. Every construction professional is familiar with the process: you drill a hole of a preferred diameter and insert an anchor, which then expands against the walls of the hole as you fasten it, creating a tight fit and locking securely in place. Although their price, wide selection, and easy installation makes mechanical anchors a fairly popular choice, they also have certain limitations that compel many construction professionals to seek alternatives. Those limitations include the need to use fastenings of a specific diameter, which in turn places a limit on possible loads, and the fact that mechanical anchors may not be used near edges, as the subsequent expansion may break it and thus destroy the construction. This is why construction professionals increasingly prefer using chemical anchors, which reduce the risk of corrosion and, thanks to bonding by adhesion, prevent splits and cracks in the base material; they may also be installed in reinforced concrete structures after casting the base. Chemical anchors also have excellent fire and seismic resistance, and can be used even in high-rise buildings, bridges, road barriers, gate systems, car servicing station equipment, and railway installations.
In individual construction projects, chemical anchors are used for securing railings, fences, poles, air conditioners, water heaters, boilers, etc. While most chemical anchors can be used in wet concrete, Tegra’s new and increasingly popular two-component Point 430 Vinyl Fix styrene-free vinylester chemical anchor, additionally, can be used for both cracked (certified for M10–M20 threaded rods) and non-cracked (M8–M30) concrete, reinforced concrete, solid (M8–M16) and hollow (M8–M12) brick masonry, and wood (M8–M16). Mechanical anchors, by comparison, may only be used for threaded rods with a diameter of up to M24. Point 430 Vinyl Fix may also be used in marine climate environments and in contact with potable water. Thanks to its strong adhesion, easy penetration into holes and hollow materials, and lack of expansion and mechanical stress, this chemical anchor may also be used to secure fixtures to corners and edges of a base material. This chemical anchor is so strong that during pull-out tests, the base concrete or the rods are almost always the first to fail.
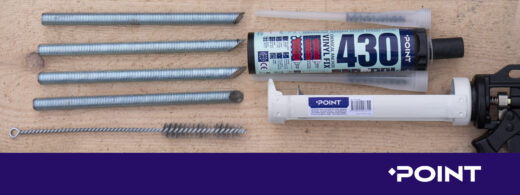
A few rules to keep in mind before chemical anchors use
Point 430 Vinyl Fix and other chemical anchors sold in Lithuania are CE certified (which is mandatory in the European Union) and ETA approved (certification for working with threaded rods). Before using a chemical anchor, one must take into account the existing environmental conditions – though in fact Point 430 Vinyl Fix may be used almost all year round, as it is compatible with base material temperatures between −10°C and 40°C. The temperature of the product itself, however, must be at least 5°C and not exceed 30°C.
Special attention should also be paid to the installation procedure. Before applying a chemical anchor, a hole is drilled perpendicular to the surface of the base material, which is then blown through using compressed air or an appropriate pump for a minimum of four times, then the hole is brushed four times, the surface-facing sides of the hole are cleaned using a steel brush, before blowing the hole through using compressed air or an appropriate pump for four more times. This level of precaution is required for a reason: without properly cleaning out the dust, the adhesive performance may be reduced by as much as 70 per cent.
Once the chemical anchor is prepared, i.e. the first 10–12 cm expelled to ensure the two components are properly mixed, two-thirds of the hole should be filled with the product. Then, a dry and clean rod should be installed into the hole by turning it forward and backward. Once the mixture hardens (the timing will depend on the surface temperature of the base material), the anchored rod is ready to receive a load. Usually, the hardening time (when the threaded rod should no longer be moved) and the time to apply a load are specified on the package.
Although chemical anchors do require some extra care during installation, construction professionals appreciate the reliable, long-lasting and high-adhesive-force bond between a construction element and the base material they create. This bond remains secure over time, as most chemical anchors are resistant to corrosion and other harsh environmental conditions.